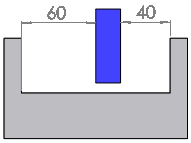 |
In this assembly model, the same degree of freedom for the blue block is defined using two distance mates, which over defines the model. Even though the mates are geometrically consistent (none of them are being violated), the model is still over defined. |