The Fill Settings define the injection molding process parameters such as Filling time, Melt temperature, Mold temperature, and Injection pressure limit.
To open the Fill Settings PropertyManager:
- In the PlasticsManager, expand Process Parameters, and click Fill Settings.
Process Parameters
Filling Time
|
Time it takes the molten plastic to fully fill the cavity. The program calculates automatically the Filling Time based on the part geometry and the properties of the material you select.
Select Auto to enable editing of the Filling Time.
If you use the Advanced options below to control the filling process, the Filling Time will be automatically re-calculated.
The diagram shows the variation of injection pressure (y-axis) with respect to filling time (x-axis). The U-shape diagram indicates that the optimal filling time is located at the bottom of the curve. For short or very long filling times, higher injection pressure values are required. 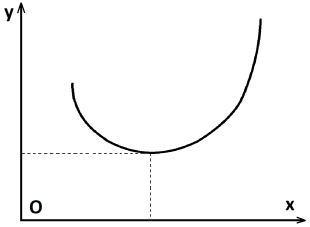
|
Melt Temperature
|
Temperature of the polymer at the injection location (or locations). The default value for Melt Temperature is taken from the material database (see Polymer-Material Parameters tab of the selected material data sheet).
Select Auto to enable editing of the Melt Temperature.
|
Mold Temperature
|
Temperature the mold is heated to. The default value for Mold Temperature is taken from the material database.
Select Auto to enable editing of the Mold Temperature.
The maximum value for Mold Temperature is 80 ºC.
If the mold temperature is not constant but varies with time, select Mold Temperature profile to enter the mold temperature data.
|
Injection Pressure Limit |
Maximum allowed value of the pressure of the polymer at the injection location (or locations). If the pressure reaches the Injection Pressure Limit value, the inlet flow rate will be automatically reduced to this limit and the Filling Time will be longer than the requested value.
You can adjust the default Injection Pressure Limit according to the capacity of your machine.
|
Advanced
|
Flow/Pack Switch Point in Filled Volume
|
Controls the process changes from FLOW to PACK. During FLOW, polymer is forced into the cavity at a given flow rate, regardless of pressure. To avoid a rapid pressure rise and potential damage to the machine, it is common to switch from FLOW to PACK just before the cavity becomes full, for example at
95% of the cavity volume.
|
|
Multi general Gate Flow-rate/Press control |
Available for shell mesh only and multiple injection locations.
Equivalent
|
Distributes equal flow rates at each injection location, with potentially different resulting pressures.
|
Automatic
|
Balances the flow between injection locations to produce equal pressures, simulating the effect of a runner system.
|
|
|
Gravity Direction: (Global) |
Defines the direction of gravity. For example, if the model is oriented in the injection molding machine such that the positive Y- axis points upwards, select the negative Y- axis for the gravity direction.
|
 |
Flow Rate Profile Settings
|
Controls the flow rate during the filling of the cavity by defining a Flow Rate Profile based either on volume or time control. |
|
Volume control (Absolute control)/Base on machine max flow rate |
You can control the variation of Flow rate or Screw speed in terms of the percentage of filled cavity volume, or the screw position. By default you can set five data pairs. You can increase the number of data pairs in Section num.
Flow rate (cc/sec) or (in3/sec)
|
Specifies the volumetric flow rate.
|
Flow rate (%)
|
Specifies the flow rate as a percentage of the Reference flow rate. For example, if the Reference flow rate (cc/sec) is 350, and the flow rate is set to 80%, then the actual flow rate will be 280 cc / sec.
|
Screw speed
|
Used together with the Screw diameter to calculate the flow rate (flow rate = Screw speed * Screw section Area).
|
Screw position
|
Used together with the Initial screw position to define the volume of material delivered to the cavity.
|
Volume (%)
|
The percentage of the filled cavity volume. You must enter a value of 100% in the last table entry.
|
|
|
Time control (Relative control)/Base on filling time |
Sets the profile of a relative flow rate versus the filling time or a percentage of the total filling time.
Filling Time (sec)
|
Displays the filling time set in the Fill Settings PropertyManager. You can enter the filling time profile data in absolute (Time sec) or relative values (Time %).
|
Flow rate (%)
|
The Flow Rate (%) values you enter in the table are interpreted relative to each other. For example, if two data points are defined with Flow Rate values of 10% and 30%, the flow rate for the second data point will be three times larger than the first flow rate value. The actual volumetric flow rates for each data point are calculated by the program to satisfy the given relative profile and the filling time for the cavity.
|
|
 |
Machine Database
|
Select an injection machine from the database. The default values for Injection Pressure Limit and Screw Bore Diameter are determined by this selection. |
|
Viscoelastic Birefringence Calculation
|
Activates the Birefringence calculation. You must select a polymer which includes definitions for the Birefringence material parameters to use this feature.
|
Solver Settings
Options
|
Provides access to the advanced solver settings. The default values are proven to produce the best results over a wide range of cases. Modifications to these values are not commonly required.
|
Fiber Orientation Calculation
To improve the strength and performance of plastic products, many plastics contain fibers. The fiber percentage of each material is included in the polymer material database. Material data, such as viscosity coefficients, reflect the properties of a particular fiber % and polymer combination.
During cavity filling, the fibers become oriented along the flow directions. This produces changes in the microstructure that affect the mechanical properties and final dimensions of the product.
Select Fiber Orientation Calculation to compute fiber orientations during the simulation.
Fiber % in Weight or Volume
|
Sets the percentage of fiber in the material based on weight or volume. For example: for 1 kg material with 200 gr of fiber, you enter 20 (%) for Weight; for 1,000 cm3 material with 100 cm3 fiber, enter 10 (%) for Volume.
|
Co-injection
In a co-injection simulation, two polymers (or a polymer and a gas) are injected sequentially into the cavity. Typically, the first material becomes skin and the second material becomes core. Co-injection is also used for Gas Assist injection molding, where a gas is selected for the second material and the part becomes hollow.
In the material dialog box, select , and select the second material from the plastics database.
2nd Material Melt Temperature
|
The default value is taken from the material database (see Polymer-Material Parameters tab of the selected material data sheet).
|
Venting Analysis
In a standard simulation, the presence of air in the cavity is ignored. Venting analysis allows you to include the effect of the air, and the pressure that it may exert on the melt front.
If you run venting analysis, you must define vent locations in the cavity (see ). Venting analysis identifies and tracks bubbles that may form and coalesce in the cavity away from air vents and computes the pressure that develops in them.
Cavity Initial Air Pressure (MPa)
|
The initial air pressure when the cavity is empty is 101,325 Pa or 0.1MPa by default. |
Cavity Initial Air Temperature ()
|
The initial air temperature in the cavity is the room temperature by default. |
Mold Temperature Profile
If the mold temperature is not constant but varies with time, select Mold Temperature profile.
Enter the mold temperature variation in terms of absolute time or as a percentage of the total process time. The total process time includes Fill, Pack, and Cool time.
For a more detailed consideration of mold temperature, you can perform a COOL simulation, where heat transfer between the cavity, mold, and cooling channels is computed. These results provide temperatures which vary both in location and in time. These COOL simulation results override any values you enter for Mold Temperature and Mold Temperature Profile.
 |
Edit/Show Profile
|
Select to set the mold temperature profile during the injection process. Enter the values of mold temperature versus time (in seconds or in percentage values of the total process time). |