Part type |
Prismatic
|
When used with Geometric as Tolerance type, DimXpert applies position tolerances to locate holes and bosses.
For annotation views, size dimensions appear as callouts with open leaders
Note the difference in the geometric tolerances applied to the 30mm boss, and the annotation view used to depict them.
|
Turned
|
When used with Geometric as Tolerance type, DimXpert applies circular runout tolerances to locate holes and bosses.
For annotation views, size dimensions appear as linear dimensions, parallel to the axis.
|
|
Tolerance type |
Controls how features of size (hole types, slots, notches, widths, and cones), pockets, and surfaces are located relative to the datum or reference features.
Plus and Minus
|
DimXpert locates the features with linear plus and minus dimensions.
DimXpert does not apply dimensions to surface features in plus and minus mode.
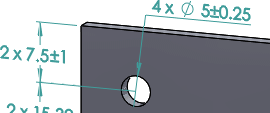 The main difference between Plus and Minus versus Geometric is how DimXpert controls the four-hole pattern, and how it applies tolerances to interrelate the datum features when in Geometric mode.
|
Geometric
|
DimXpert locates axial features with position and circular runout tolerances. Pockets and surfaces are located with surface profiles.
To show location dimensions, you must select , and then select Create basic dimensions.
|
|
Pattern Dimensioning |
Lets you apply linear or polar plus and minus dimension schemes.
Linear
|
Locates all DimXpert features relative to the selected reference features, as applicable, using linear plus-minus dimensions.
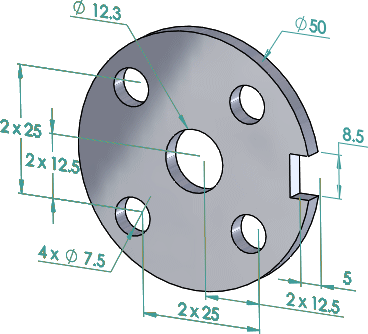
|
Polar
|
Apply to DimXpert pattern features that contain axial features that define a bolt circle.
Set the Minimum number of holes to recognize as a pattern.
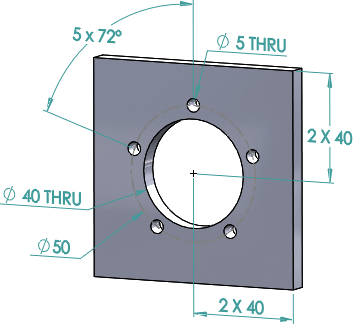
|
|