Not all stress hot spots are associated with stress singularities. Refining locally the mesh at hot spot regions can eliminate these stress hot spots attributed to stress concentrations that are nonsingular.
A characteristic behavior of a stress singularity is that the stress value keeps increasing with mesh refinement (either locally using mesh controls or globally by editing the mesh), and is diverging theoretically to infinity. If the stresses at the elements of stress hot spots do not increase with mesh refinement and converge towards a finite value, then they are indicative of stress concentrations (areas of 'legitimate' high stresses).
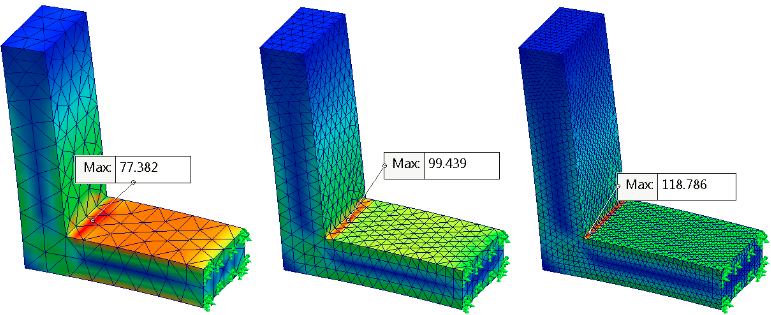 |
Diverging stresses near sharp re-entrant corner as the mesh gets refined are indicative of stress singularities. |
Stress concentrations are characterized by relatively large stress gradients over adjacent elements at a localized area of a model. High stress gradients attributed to legitimate stress concentrations will converge to a limit value given that the mesh is sufficiently refined. They are visible where there are changes in geometry, such as a presence of a hole in a plate, at boundaries where different materials are present, and at points where bodies come into contact.
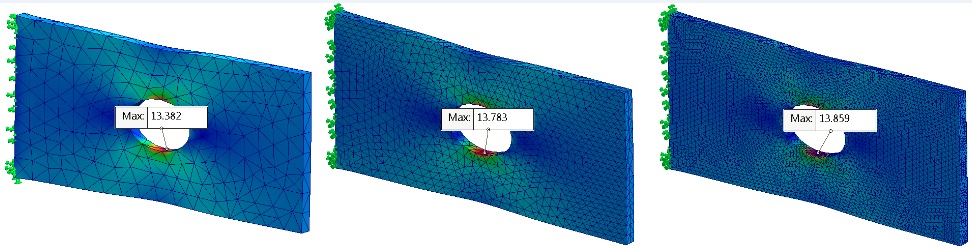 |
Converging stresses near the hole as the mesh gets refined are indicative of stress concentrations. |
You can find tabulated data in literature with stress concentration factors of maximum stress / nominal stress for problems with analytical solutions (Young, W., Budynas, R., (2001), Roark’s Formulas for Stress and Strain, Chapter 17 – Stress Concentration Factors for Elastic Stress (Kt))
Recommendations on Treating Stress Singularities
-
To differentiate stress singularities from legitimate stress concentrations, refine the mesh either globally, or locally at the regions where stress hot spots are detected. When you rerun the stress hot spot diagnostics tool, the areas of stress concentrations should be filtered out, and the remaining stress hot spots would point to stress singularities. Note that in the physical world, stress singularities do not occur as the material will yield or crack when stresses exceed the material's ultimate strength limit.
- Add fillets to sharp edges and “round off” corners where high stress gradients occur. The fillets distribute the stress over a broader area and effectively increase the load bearing capacity of parts. Remember that in the real world a manufactured “sharp corner” will always have a small fillet radius.
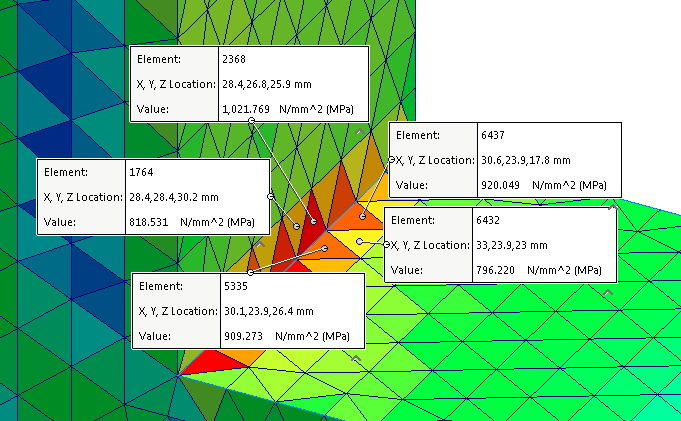 |
Irregular stress distribution at sharp edges. |
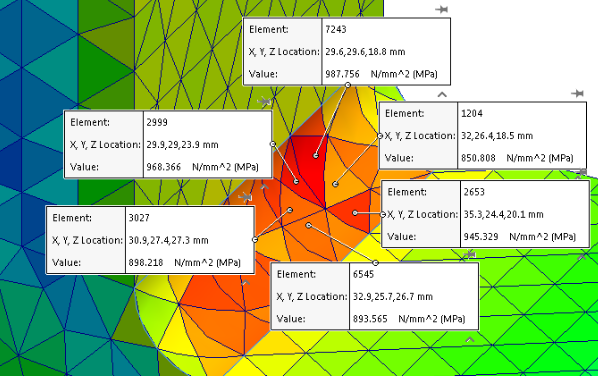 |
Smooth stress distribution at fillet corner. |
-
Avoid applying loads on vertices or along edges, if you can. Distribute the load to the proper tributary areas on the model to approximate as accurately as possible the real loading conditions. Remember that even if the load is applied as a singular point load creating a stress singularity (σ = P/A and A=0 → σ=∞), the stress distribution some distance away from the applied load will still be correct. This is based on the St. Venant’s principle that states that the difference between the effects of two different but statically equivalent loads becomes very small at sufficiently large distances from the load.
- Stress singularities can pollute stress distributions only locally. You may ignore these localized areas of stress singularities, especially if they are not near the area of interest in your simulation, and examine the stress results further away which should remain "unpolluted".