You can include temperatures and pressures calculated in previous thermal or SOLIDWORKS Flow Simulation studies in a static, buckling, frequency, or nonlinear study.
If an unrestrained body is subjected to a change in temperature, it will expand or contract freely as it is heated or cooled. The change in temperature causes strains but no stresses. If the body is prevented from expansion or contraction freely, stresses are induced. The induced stresses are equivalent to those required to deform an equivalent unrestrained body similarly.
It is important to include the contribution of temperature changes to stresses for restrained models. The coefficient of thermal expansion material property is required to consider this effect. You need to specify the reference temperature (T0) associated with the stress-free condition.
You specify the average coefficient of thermal expansion in the material properties.
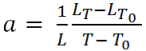
The program uses the acquired temperatures for two purposes:
- thermal loading
- temperature-dependent material properties for each element where the temperature for each element is calculated by averaging the temperatures of its nodes.
Temperatures can be input directly as prescribed temperatures, imported from the results of a Thermal study, or imported from the results of a SOLIDWORKS Flow Simulation study. Pressure loads can also be imported from the fluid pressure results of a SOLIDWORKS Flow Simulation study.
SOLIDWORKS Flow Simulations must be performed on solid or sheet metal bodies. If the active study contains shell surfaces created from solid faces, temperature or pressure values from the original solid faces are mapped onto the surface shell mesh. The shell thickness and offset must correspond with the original solid geometry in the Flow Simulation mesh.
For proper acquisition of temperature and pressure loads from Flow Simulation, the active study and the Flow Simulation study should be associated with the same configuration.
When you include temperatures and pressures in a nonlinear study, you must specify how these loads vary over the course of the solution period.
- If you acquire a single temperature profile, or pressure profile from SOLIDWORKS Flow Simulation, the program associates it automatically with the default linear curve. The temperature profile is varied linearly until it reaches the acquired values at the end of the solution period.
- If you select a transient flow problem from SOLIDWORKS Flow Simulation, specify a particular time step to acquire the temperatures. The temperatures are applied linearly as specified by the solution time parameters.
- If you select a transient thermal study, you have two options:
- Specify a particular time step to acquire the temperatures. The temperatures are applied linearly as specified by the solution time parameters.
- For each nonlinear step, use temperature from corresponding time of transient thermal analysis.
The meshes of the thermal and nonlinear studies must be identical. For this functionality to work properly, the time range for the solution should be similar for the thermal and nonlinear studies. Using a different time range for the nonlinear study may lead to incorrect results.