The Pack analysis module simulates the conditions inside the cavity
before
part ejection.
SOLIDWORKS Plastics simulates the material’s phase change from fluid to solid
and the volumetric shrinkage that results. It also simulates the build-up of stresses,
which later influence the molded plastic part’s final dimensions and
warpage. Pack results
are required to run a Warp analysis.
Pack
analysis
simulates the process where an injection machine applies pressure to
the injection system to cause additional material to enter the cavity as the part
shrinks and freezes. To control the switch-over from Flow to Pack, you can specify a
time value or a cavity fill percentage in the Pack
Settings PropertyManager. You can also use these settings to create a
pressure profile rather than using a constant packing pressure.
Results from a Pack analysis include:
- Distributions of temperature time histories at every
location
of the part, which allows the prediction of hot spots, gate freeze, and cycle
time
- Distributions of pressure, residual stress, and volumetric
shrinkage
- Information about the required clamping force and the
time-evolution of the part mass as the material density changes.
From the Flow and Pack analyses, you can estimate the optimal process
conditions, such as filling time, injection pressure profile, pressure holding time,
melt temperature, and mold temperature. In addition, you can gain insights about the
optimal mold design parameters such as gate location, gate design, and runner
design.
Pack Analysis Steps
1 |
Define the process parameters:
- Pack time, pressure profile
- Pure cooling time
|
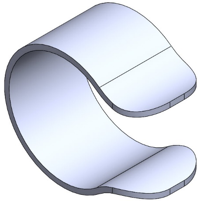 CAD geometry of a
part |
2 |
Create the mesh and select
materials |
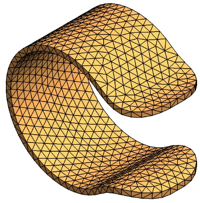
Surface mesh
|
3 |
Run the analysis |
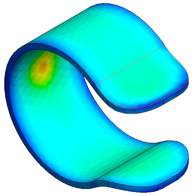
Result plot of volumetric shrinkage at end of
packing
|