Connector - Bolt
A Bolt
can connect
two components, multiple components, or a component and the ground. You
can define bolts through a mixed stack of solids, shells and sheet metal
bodies.
Type
Bolt Type |
Options |

Standard or Counterbore
with Nut |
Circular Edge
of the Bolt Head Hole and Circular
Edge of the Bolt Nut Hole . Select an edge to define
the bolt head and bolt nut location, respectively.
Same head and
nut diameter. Select if the bolt head is the same diameter as the
nut.
Head Diameter
and Nut Diameter
. Set the units and value of the diameter of the bolt
head and bolt nut, respectively. By default, the program multiplies the
shank diameter by a factor of 1.5 to obtain the head diameter.
Bolt Shank Diameter
. Set the units and value of the diameter of the shank.
|

Countersink with Nut |
Conical Face
. Select a conical face to define the bolt head.
Circular Edge
of the Bolt Nut Hole . See earlier description.
Nut Diameter
and Bolt Shank Diameter
. See earlier description. By default, the program
multiplies the shank diameter by a factor of 1.5 to obtain the nut diameter.
|

Standard or Counterbore
Screw |
Circular Edge
of the Bolt Head Hole . See earlier description.
Thread Face(s)
. Select the hole faces from another component in contact
with the threads.
Head Diameter
and
Bolt Shank Diameter . See earlier description. By default, the program multiplies
the shank diameter by a factor of 1.5 to obtain the head diameter.
|

Countersink Screw |
Conical Face
. See earlier description.
Thread Face(s)
. See earlier description.
Bolt
Shank Diameter . See earlier description.
|

Foundation Bolt |
Circular Edge
of the Bolt Head Hole . See earlier description.
Target plane
. Select a plane to model a virtual wall. You must define
a Virtual Wall contact condition to prevent penetration into the foundation.
Nut Diameter
and Bolt Shank Diameter
. See
earlier description. By default, the program multiplies the shank diameter
by a factor of 1.5 to obtain the nut diameter.
|
The value for Bolt
Shank Diameter
should be equal to or less than the
diameters of the Thread face(s).
Tight Fit
Select if the radius of the shank is equal
to the radius of the cylindrical faces associated with at least one of
the components. A cylindrical face set to Tight
Fit is rigid and deforms with the shank as a rigid body. Example of a tight fit bolt connector.
Shank Contact
Faces
. Select one or more cylindrical faces that
are in contact with the shank. If you select multiple faces from a component,
they must have the same axis and radius.
Material
Simulation selects Alloy steel from the SolidWorks
Material library as bolt material by default.
The program does not maintain a link to the selected
library. If you edit the library, the changes are not reflected for the
bolt.
Strength Data
Known tensile
stress area. Select this option if the tensile stress area (minimum
area of the threaded section of the bolt) is known.
Calculated tensile
stress area. Select this option to let the program calculate
the tensile stress area of the bolt.
Tensile Stress
Area. Set the known tensile stress area for the bolt.
Thread Count.
Enter the number of threads per inch, or per millimeter measured along
the length of the fastener.
Bolt Strength.
Set the strength of the bolt's material and its unit.
There are three commonly used
strength parameters for bolts to estimate bolt failure. Yield strength,
Ultimate Strength and Proof Strength (90% of Yield strength). The most
commonly used parameter is the Yield strength of the bolt's material or
grade, but users should choose a strength value that is most appropriate
for the application.
Pre-load
Friction
Factor (K)
. The program uses this factor to calculate
the axial force from a given torque.
Advanced Option
. Select the cylindrical
faces of solid bodies or circular edges of shell surfaces from the middle
components. For nonlinear studies, select a cylindrical face from a solid
body.
Reference
Geometry
. For 1/2 symmetry bolts, select the plane
or planar face of symmetry.
If you use symmetrical bolts,
enter 1/2 or 1/4 of the total pre-load value and 1/2 or 1/4 of the total
mass of the bolt according to the selected symmetry type. Also, when you
list bolt forces after running a study, the results equal 1/2 or 1/4 of
the total force.
Symbol Settings
Edit
color. Select a color for the symbols.
Symbol Size
. Set the size of the symbols.
Show preview. Toggle the visibility of the bolt in the
graphics area.
Notes
Available for static and nonlinear studies.
The bolt connector formulation is an approximation
of a complex nonlinear behavior. It provides accurate results when the
bolts are under tension. In loading scenarios where the bolts are under
compressive loads, the axial forces of bolt connectors may not be accurate.
In such cases, a decrease in preload bolt force can result in a "loosening"
of the bolt and loss of contact between the bolt and the components. This
behavior cannot be captured by the bolt connector formulation in Simulation.
For these cases, model the actual bolt and define no penetration contact
sets between the bolt and the components.
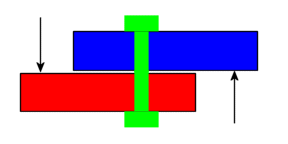
|
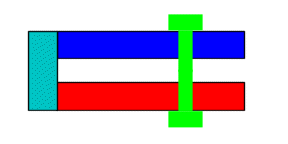
|
Define contact between these
two faces. You can define a global, component, or a local contact. |
You do not need to define contact
when the faces are not initially contacting and do not come into contact
during loading. |