The Thread tool provides many options for creating helical threads on cylindrical bodies. Sometimes interactions of the options can cause subtle errors. You can avoid these errors by following these guidelines.
Create exactly one vertical centerline that starts from the origin.
SOLIDWORKS uses only one vertical centerline to define the pitch of the thread, and will ignore a others. If you draw more than one centerline you may have trouble keeping track of which one is being used.
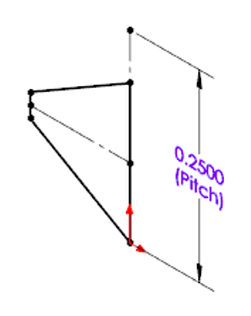
Make sure the centerline is taller than the profile.
Make sure that the centerline is taller than the profile. The height of the pitch must be greater than the profile between the revolutions to ensure that revolutions do not intersect with each other.
Pitches are defined differently in inches and metric units.
When you define threads in inches, pitches are defined in terms of revolutions per unit of measure (for example, threads per inch).
When you define threads in metric units, pitches are defined in terms of units of measure per revolution (for example, millimeters per thread).
If you don’t create a centerline, SOLIDWORKS assumes a pitch of one revolution per model unit length (such as, one thread per inch or one millimeter per thread).
Create only one closed contour in a sketch.
SOLIDWORKS can only use one closed contour to define a thread. Creating more than one closed contour in a sketch causes an error.
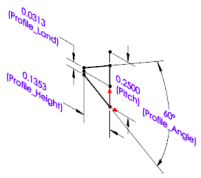 |
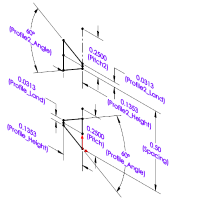 |
One closed contour allowed |
Multiple contours are invalid |
Only one active sketch in a configuration is allowed.
SOLIDWORKS uses the first active sketch and ignores any others. Suppress all of the sketches but one, so you do not have trouble keeping track of which one is being used to create the thread.
You can override the default diameter and pitch, but be careful.
The Thread PropertyManager includes inputs where you can override the default diameter and pitch. Be careful that your changes do not create an error, for example (by defining a diameter for the thread that is inconsistent with the diameter of the cylinder). If you make a mistake, you can return the diameter and pitch to the default values by using the pitch override controls.
Do not assume too much from a profile name.
Profile names are representative of the profile shape, but not necessarily of the geometry they create. Do not assume that a profile name tells you much about the final geometry of the thread.
Use Library Feature Parts to create profiles.
Profiles created from scratch need to be made using the Library Feature Part methods or use a profile provided with the SOLIDWORKS software to start with.
The default directory for storing thread profiles is C:\ProgramData\SolidWorks\SOLIDWORKS YYYY\Thread Profiles.
Be careful with spatial relationships, especially with cut and offset.
Be careful that you do not change profiles in ways that make the thread inconsistent with the underlying shape. For example, you may have a profile with a cut thread that works well on shafts, but cannot be applied to holes (you might need to change to extrude for a hole). Or, you might have a profile that works fine, but the offset it just far enough to lose contact with the underlying shaft. If you receive an error after changing the offset, reverse the change and try a smaller value for the offset.
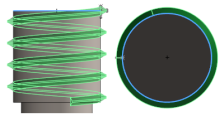 |
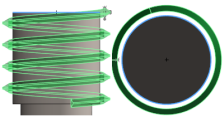 |
In context |
Out of context |