The yield criterion can be written in the form:
where

is the effective stress and σ
Y is the yield stress from uniaxial tests. The von Mises model can be used to describe the behavior of metals. In using this material model, the following considerations should be noted:
- Small strain plasticity is assumed when small displacement or large displacement is used.
- An associated flow rule assumption is made.
- Both isotropic and kinematic hardening rules are available. A linear combination of isotropic and kinematic hardening is implemented when both the radius and the center of yield surface in deviatoric space can vary with respect to the loading history.
The parameter RK defines the proportion of kinematic and isotropic hardening. For pure isotropic hardening, the parameter RK has the value 0. The radius of the yield surface expands but its center remains fixed in deviatoric space. For pure kinematic hardening, the parameter RK has the value 1. The radius of the yield surface remains constant while its center can move in deviatoric space.
A bilinear or multi-linear uniaxial stress-strain curve for plasticity can be input. For bilinear stress-strain curve definition, the yield strength, elastic modulus, and tangent modulus are input through the Material dialog box. For multi-linear stress-strain curve definition, a stress-strain curve should be defined.
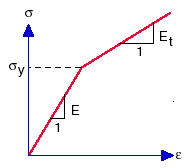
When you define a stress-strain curve, the first point on the curve should be the yield point of the material. Material properties like elastic modulus, Yield strength, etc will be taken from the stress-strain curve when it is available and not from the material properties table in the Material dialog box. Only Poisson's ratio (NUXY) will be taken from the table.
Drop test studies can only use bilinear stress-strain curves for plasticity. If you define a multi-linear stress-strain curve and run a drop test study, the solver will ignore it.
The yield strength and elastic modulus parameters for bilinear stress-strain curve description can be associated with temperature curves to perform thermoplastic analysis. Thermo-plasticity is not available with shell elements.
The Huber-von Mises model can be used with the solid (draft and high quality) and thick shell (draft and high quality) elements.
The use of the NR (Newton-Raphson) iterative method is recommended.
Typical stress-strain curve of a plastic material:
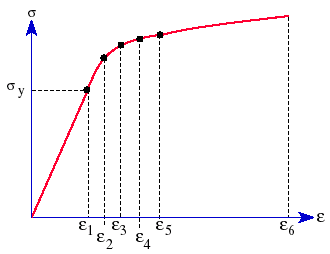