The improved pin connector is extended to nonlinear static and nonlinear
dynamic studies. You can define a pin connector through more than two cylindrical surfaces
in one definition.
You can define a single pin connector attached to multiple coaxial cylindrical
faces (maximum ten).
In the Connector-Pin
PropertyManager, for Cylindrical Faces/Edges
, select all coaxial cylindrical faces
(or edges) that are attached to the pin (maximum of ten). The selected cylindrical faces
or circular edges can belong to one body or to several bodies.
For example, for the two models below, you can define two pins (one for each
model) to connect the two rotating parts and the six cylinders of a hinged plate. You
can then run a nonlinear static or nonlinear dynamic study.
The solver calculates the pin connector forces at two pin joints per pin
segment (a pin segment attaches to two cylindrical faces.) The safety factor for each
pin connector is calculated based on the least FOS at the pin joints for the selected
pin connector. The total axial and rotational stiffness you define for a pin connector
is distributed according to each pin segment's geometric characteristics such as: cross
sectional area, length, and polar moment of inertia.
For example, for a single pin definition connecting four cylinders of a hinged
plate, the solver calculates the pin forces at four pin joints. Each pin joint is
located at the centroid of each cylindrical face attached to the pin.
When viewing pin connector results, in the Result
Force PropertyManager, click a table cell under Connector Force to highlight the location of the
selected pin joint. A callout lists the pin forces at the selected joint. The directions
of the pin resultant forces with respect to the pin's local coordinate system are also
displayed: shear force resultant, axial force resultant, bending moment resultant, and
torque resultant.
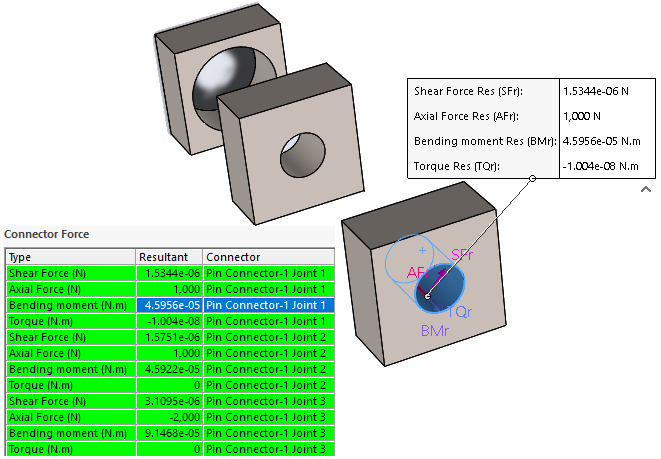
Click List X,Y,Z components to
list the X, Y, and Z components of the pin forces with respect to the global coordinate
system.