Polymer |
Melt
Temperature |
Defines the material manufacturer’s recommended
temperature of the polymer as it exits the molding machine through the
nozzle and enters the mold. Minimum and maximum values define the
manufacturer’s allowable range. |
Polymer |
Mold
Temperature |
Defines the material manufacturer’s recommended
temperature of the mold during injection. Minimum and maximum values
define the manufacturer’s allowable range. |
Polymer |
Ejection
Temperature |
Defines the temperature of the part when it has
cooled down and is ready for ejection. |
Polymer |
Transition
Temperature |
Defines the temperature at which a polymer changes
from melted to solid state. For semicrystalline materials, this is a
precise temperature. For amorphous materials, the transition occurs
gradually over a range of temperatures, but is given as a single
value. |
Polymer, and
Coolant |
Viscosity |
Defines a measure of a melted polymer's resistance to
a flow. Highly viscous fluids, like peanut butter, resist a flow much
more than low viscosity fluids like water. Most polymers are
non-Newtonian, which means their viscosity is dependent on the shear
rate they experience. Polymers solidify as they cool, so their viscosity
also depends on temperature. |
Polymer, and
Coolant |
PVT(pressure,
volume, temperature) |
Defines the relationship between pressure, volume,
and temperature parameters that evaluate how much a polymer shrinks as
it cools from melted to solid state during the injection molding
process. |
Polymer, and
Mold |
Solid
Density |
Defines the mass-per-unit volume of a material in its
solid state. |
Polymer,
Mold, and Coolant. |
Specific
Heat |
Defines the amount of energy required to heat one
kilogram of a material by one Kelvin. |
Polymer,
Mold, and Coolant |
Thermal
Conductivity |
Defines a measure of how easily thermal energy can
transfer through a material. |
Polymer,
Mold |
Elastic
Modulus |
Defines a measure of a material's resistance to
deform elastically under stress application. More specifically, the
ratio of tensile stress to tensile strain (also known as Young's
modulus). |
Polymer,
Mold |
Poisson's
ratio |
Defines the ratio of transverse contraction strain to
longitudinal extension strain in the direction of the stretching
force. |
Polymer,
Mold |
Thermal Expansion
Coefficient |
Defines a measure of how a material expands and
contracts because of changes in temperature. |
Polymer |
Shear Relaxation
Modulus |
Defines a measure of how a material relieves stress
over time when subjected to constant strain. |
Polymer |
Curing
Model |
Describes the curing process for a thermoset
material. |
Polymer |
No-Flow
Temperature |
Defines the temperature at which a polymer no longer
flows. |
Polymer |
Melt Flow
Rate |
Defines a measure of the ease of flow of a melted
polymer. |
Polymer |
%
Fiber |
Defines the percentage of fiber filler by
weight. |
Polymer |
Max Shear
Rate |
Defines the material manufacturer’s maximum allowable
shear rate. |
Polymer |
Max Shear
Stress |
Defines the material manufacturer’s maximum allowable
shear stress. |
Polymer |
Stress Optical
Coefficient |
Defines a measure of the amount of birefringence
because of residual stress in a transparent polymer. Birefringence is the optical property of a material having a
refractive index that depends on the polarization and propagation
direction of light.
|
Polymer |
Leonov
Parameters |
Defines the parameters of the Leonov Viscoelastic
Model used to predict birefringence. Viscoelastic materials exhibit both
viscous and elastic behavior under stress. Material deformation is
temporary when the stress is removed quickly, but permanent when the
stress is sustained. |
Polymer |
WLF
Parameters |
Defines the Willams-Landel-Ferry (WLF)) equation
coefficients for the Leonov Viscoelastic Model. The
WLF equation is: 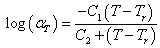
where T is the
temperature, Tris a reference
temperature, and C1 and C2 are empirical constants.
|
Polymer, and
Mold |
Shear Modulus |
Defines the in-plane ratio of shear stress to shear strain.
If the Shear Modulus (G12) of a material is not available, an
approximate value for G12 is considered in the analysis. The
approximate value is calculated based on the methods published
in “Introduction to Composite Materials Design,” Second Edition,
by E. J. Barbero.
|
Polymer |
Crystallization
Kinetics |
Defines a measure of the crystallization process of a
semicrystalline polymer that occurs between its melting point and
glass transition temperature.
|
Polymer |
Juncture Loss
Coefficients |
Defines a measure of the hydraulic loss experienced
when a polymer flows through a significant change in cross-sectional
area, such as those common to a runner system. |
Polymer |
Data Source and
Information |
Indicates the source of the material data and any
additional grade-specific information. |