When loads are applied to a body, the body tries to absorb its effects by developing internal forces that, in general, vary from one point to another. The intensity of these internal forces is called stress. The units of stress are force per unit area.
Stress Components
Consider a bar under compression. The state of stresses at point P can be described in terms of an arbitrary plane. Although the resultant stress is always the same, the values of the stress components depend on the chosen plane.
Stress is described by magnitude, direction, and the plane on which it acts. The state of stresses at a point is fully described by the following components:
SX
|
Stress in the X-direction acting normal to the YZ-plane
|
SY
|
Stress in the Y-direction acting normal to the XZ-plane
|
SZ
|
Stress in the Z-direction acting normal to the XY-plane
|
TXY
|
Stress in the Y-direction acting on the plane normal to the X-direction (YZ-plane)
|
TYX
|
Stress in the X-direction acting on the plane normal to the Y-direction (XZ-plane)
|
TXZ
|
Stress in the Z-direction acting on the plane normal to the X-direction (YZ-plane)
|
TZX
|
Stress in the X-direction acting on the plane normal to the Z-direction (XY-plane)
|
TYZ
|
Stress in the Z-direction acting on the plane normal to the Y-direction (XZ-plane)
|
TZY
|
Stress in the Y-direction acting on the plane normal to the Z-direction (XY-plane)
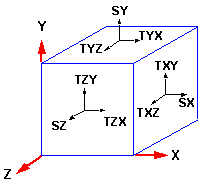
|
SX, SY, and SZ are called normal stresses. TXY, ...., TZY are called shear stresses. Shear stresses are related by the following equations: TXY = TYX, TXZ = TZX, and TYZ = TZY. Thus, the stress state at a point is completely defined by six components.
Principal Stresses
For each point, there is a plane on which there are no shear stresses. The state of stresses in reference to this plane is defined completely by normal stresses, called principal stresses.
P1
|
Normal stress in the first principal direction (largest).
|
P2
|
Normal stress in the second principal direction (intermediate).
|
P3
|
Normal stress in the third principal direction (smallest).
|
|
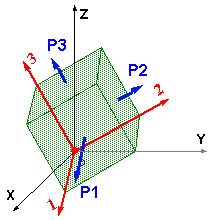
|
Equivalent Stress (also called von Mises Stress)
In SimulationXpress, you view a stress quantity called the equivalent (or von Mises) stress. While the equivalent stress at a point does not uniquely define the state of stress at that point, it provides adequate information to assess the safety of the design for many ductile materials.
Unlike stress components, the equivalent stress has no direction. It is fully defined by magnitude with stress units. To calculate the factors of safety at different points, SimulationXpress uses the von Mises Yield Criterion, which states that a material starts to yield at a point when the equivalent stress reaches the yield strength of the material.