A 50X50X8 mm Silicon chip is joined to a 50X50X12 mm Aluminum substrate by a 0.2-mm-thick epoxy layer. The upper surface of the chip and the lower surface of the Aluminum substrate are exposed to a forced airflow for cooling.
Here are numerical values of the problem parameters:
- Temperature of cooling air = 25 °C
- Convective heat transfer coefficient = 250 W/m2K
- Thermal contact resistance per unit area of the chip = 1X10-4 m2K/W
- Thermal conductivity of the Silicon Chip = 1800 W/m.K
- Thermal conductivity of the Aluminum Substrate = 240 W/m.K
- Heat power generated in the Chip = 25 Watts
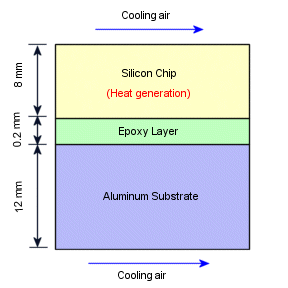
In simulating this problem, the epoxy layer is neglected. The faces of the chip and the substrate, separated by the epoxy layer, are mated as coincident. The effect of the epoxy layer is defined by a distributed thermal resistance between the contacting faces.
An analytical solution is available for this problem.
The
analytical solution assumes that the chip has a constant temperature at all its
points (isothermal). To simulate this assumption, an artificially high conductivity
of 1800 W/m.K is specified for the chip. Highly conductive materials tend to be
isothermal. The actual conductivity of Silicon is much smaller than this value.