The Cool analysis module performs heat transfer analysis to obtain the
transient
temperature
distribution
occurring within the
mold during the injection
molding
cycle.
The Cool analysis encompasses the mold, the cavity, and the cooling system within the
mold. Temperature changes occur slowly compared to the speed at which the cavity
fills.
SOLIDWORKS Plastics makes an approximation that allows running the Cool
analysis first, separately from the Fill analysis module. It stores the transient
temperature results from the Cool analysis in a database for use in subsequent Fill and
Pack simulations.
To simplify the problem, you can
skip
the Cool analysis, and enter mold temperature data as a single uniform value for the
entire cavity surface using the Fill Settings
PropertyManager. You can also select surfaces and specify their temperature values using
the Mold Wall Temperature boundary condition.
Cool Analysis Steps
1 |
Define the process parameters:
- Cooling channels geometry
- Mold dimensions
- Melt temperature
- Coolant temperature and Flow rate
profile
|
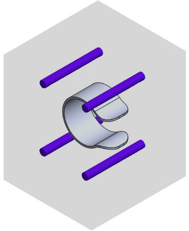 CAD geometry of a
mold, cooling channels, and part |
2 |
Create the mesh and select
materials |
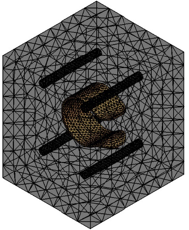
Surface mesh
|
3 |
Run the analysis |
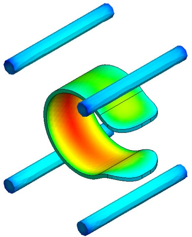
Result plot of average mold temperature at the
end of cooling
|