The program bonds the Set 1 and
Set 2 (source and target) entities defined in
the Local Interactions PropertyManager. Bonded
entities behave as if they were welded. For geometric entities that mesh independently,
bonding is applied with constraint equations.
You also have the option to bond components by enforcing common mesh
nodes at their boundaries. In this case, the components that have common mesh nodes at
their boundaries mesh as one body.
You can apply bonded interactions to these simulation studies:
- Static
- Frequency
- Buckling
- Thermal
- Nonlinear
- Dynamic
- Drop test
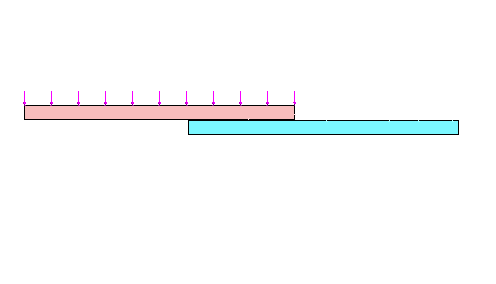 |
Bonding between components that are touching (no
clearance). |
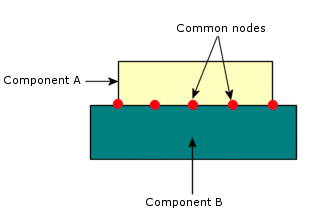 |
Illustration of common mesh nodes at component boundaries. The
two components mesh as one body. |
This limitation applies only to (a) the node-to-surface bonding
formulation for all studies, and (b) the surface-to-surface bonding formulation for
nonlinear studies.
In cases where bonding contact exists between sheet metal parts
with other surfaces (solids or shells), the bonding algorithm can enforce
over-stiffening due to the gap between the mid-surface mesh and the contact surface
geometry. The over-stiffening of the bonding contact alters the calculation of the
rigid body modes. The program will calculate all rigid modes (with frequency values
close to 0), if you eliminate the gap by offsetting the mesh of the sheet metal
parts from the mid-surfaces to the contact surface geometry.