Fatigue - Options
The Options tab of the Fatigue dialog box allows you to set
options for the active fatigue study.
You can define studies with constant amplitude
events or variable amplitude events. You cannot mix constant and variable
amplitude events in a study.
The ASME Boiler and Pressure
Vessel recommends this option. It is
more conservative (predicts higher damage) than the No interaction option.
For studies with fatigue
events referencing to multiple studies, the program calculates peak stresses
based on the Random option even if you select the No interaction option.
Using a large number distorts the variable amplitude
record and results in underestimating the damage. For accurate damage
prediction, the highest alternating stress filtered out should not be
larger than the equivalent endurance limit of any
associated S-N curve.
These methods are used only
if all associated S-N curves are based on fully reversible environment
(zero mean). The software calculates the mean stress in addition to the
alternating stress for each cycle and then it evaluates the corrected
stress using the specified method. The correction becomes significant
if the applied fatigue load cycles have large mean stresses compared to
the stress range. If you define multiple S-N curves with different load
ratios, the program interpolates between the curves linearly to account
for mean stresses and no correction method is used. If you define one
S-N curve with a stress ratio other than -1 for a material, the curve
is used without correction for that material.
Fatigue
strength reduction factor (Kf). Use this factor, between 0 and
1, to account for differences in test environment used to generate the
S-N curve and the actual loading environment. The program divides the
alternating stress by this factor before reading the corresponding number
of cycles from the S-N curve. This is equivalent to reducing the number
of cycles that cause failure at a certain alternating stress. Fatigue
handbooks suggest numeric values for the fatigue strength reduction factor.
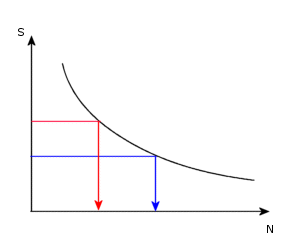
This value is only used for S-N curves for which the
maximum number of cycles is less than the specified number.
Related Topics
Remark
Tab
What
is Fatigue Analysis...