Remesh failed parts with incompatible mesh |
Tries to use incompatible meshing for bonded bodies that fail compatible meshing.
Used for solid mesh only.
|
Curvature based |
Activates the curvature-based meshing scheme for subsequent meshing operations.
The mesher creates more elements in higher-curvature areas automatically (without need for mesh control). |
The curvature-based mesher can check for interference between bodies before meshing.
If interferences are detected, meshing stops and you can access the Interference Detection PropertyManager to view the
interfering parts or components. Make sure to resolve all interferences before you mesh again.
Interference detection is only available when you define bonded contact with compatible mesh.
Curvature-based mesh is always compatible for touching or partially touching edges of sheet metal bodies and surface bodies.
The curvature-based mesher also supports compatible meshing between touching solid faces.
|
Default number of elements on a circle |
Sets the minimum number of elements the mesher creates at curvatures.
See How Element Size Is Determined. |
Standard |
Activates the Voronoi-Delaunay meshing scheme for subsequent meshing operations. |
Automatic transition |
Automatically applies mesh controls to small features, holes, fillets, and other fine details of the model. Clear Automatic transition before meshing large models with many small features and details to avoid generating unnecessarily large numbers of elements.
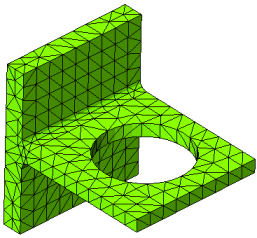 |
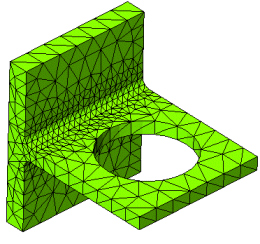 |
Automatic transition OFF
|
Automatic transition ON
|
|
Automatic trials for solids |
Automatically retries to mesh the model using a different global element size. You control the maximum number of trials allowed and the factors by which the global element and tolerance are scaled for each trial. |
Number of trials |
Sets the maximum number of mesh trials. |
Factor for element size for each trial |
Sets the multiplying factor to calculate the new global element size. |
Factor for tolerance for each trial |
Sets the multiplying factor to calculate the new tolerance. If the distance between two nodes is smaller than this value, the nodes are merged unless otherwise specified by contact conditions.
The tolerance cannot exceed 30% of the element size.
|