Linear static analysis assumes that the relationship between loads and the induced response is linear. For example, if you double the magnitude of loads, the response (displacements, strains, stresses, reaction forces, etc.), will also double.
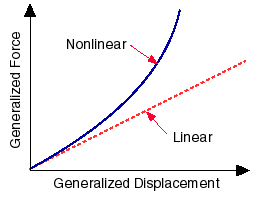
All real structures behave nonlinearly in one way or another at some level of loading. In some cases, linear analysis may be adequate. In many other cases, the linear solution can produce erroneous results because the assumptions upon which it is based are violated. Nonlinearity can be caused by the material behavior, large displacements, and contact conditions.
You can use a nonlinear study to solve a linear problem. The results can be slightly different due to different procedures.
In the nonlinear static analysis, dynamic effects like inertial and damping forces are not considered. Processing a nonlinear study differs from processing a static study in the following ways:
Study Properties
The Nonlinear
dialog box includes four tabs: Solution, Advanced Options, Flow/thermal Effects, and Remarks. The Solution and Advanced tabs set options and parameters related to the numerical procedures to be used in solving the problem. The Flow/Thermal Effects and Remarks tabs are similar to those in the static study properties dialog box.
For nonlinear static analysis, the time is a pseudo variable. It describes at what load levels the solution is sought. Only for visoelastic and creep material models, the time has real values. For nonlinear dynamic analysis, the time is a real value.
Material
For static studies, you can only select linear isotropic and linear orthotropic materials. For nonlinear studies, you can define the following material models, in addition:
- Nonlinear Elastic
- von Mises Plasticity (kinematic & isotropic)
- Tresca Plasticity (kinematic & isotropic)
- Drucker Prager Plasticity
- Mooney Rivlin Hyperelastic
- Ogden Hyperelastic
- Blatz Ko Hyperelastic
- Viscoelastic
Loads and Restraints
When the force control method is used, restraints and loads are defined as functions of time. For visco-elasticity and creep problems, as well as nonlinear dynamic analysis, time is real. For other problems, time is a pseudo variable that specifies the load level at different solution steps.
Displacement control uses the curve that is associated with the controlling DOF only. The Arc Length control method does not use any time curves.
Solution
The solution of nonlinear studies involves calculating the results at different solution steps (load and restraint levels). The numerical procedures are more complex than the solution of linear static studies. In seeking convergence to the correct solution at a solution step, the program performs a number of iterations. For these reasons, the solution of nonlinear studies is much more time consuming and resource demanding than the solution of linear static studies.
Although the program calculates results at different solution steps, it only preserves the results at the last solution step by default. You can select certain locations and solution steps at which results are preserved as part of defining properties of the study.
Results
Results are available as functions of time. For example, stresses are available at different solution steps. In addition to viewing the results at the last solution step, you can view results at other solution steps requested in the properties of the study for the solution. For locations selected in the properties of the study, you can graph results as function of pseudo time (load history).
Contact Problems
Contact is a common source of nonlinearity. Static studies allow the solution of contact problems with small and large displacements. The following are limitations on using static studies to solve contact problems:
- If you use large displacements, the results are available only at the last solution step. In nonlinear studies, you can get results at every solution step.
- If a nonlinearity other than that caused by contact is present, you cannot use static studies. This can be due to nonlinear material properties, changed loads, or restraints, or any other nonlinearity.
- When using static studies to solve contact problems with large displacements, the program does not update the load directions as the model deforms. In nonlinear studies, the program updates the directions of pressure loading based on the deformed shape at each solution step if the Update load direction with deflection is checked in the properties of the study.
In nonlinear studies, you have control over the solution steps. In static studies using large displacements, the program sets the solution steps internally.