SOLIDWORKS SimulationXpress offers an easy-to-use first pass stress analysis tool for SOLIDWORKS users. SimulationXpress can help you reduce cost and time-to-market by testing your designs on the computer instead of expensive and time-consuming field tests.
For example, you might want to examine the effects of a force applied to the faucet. SimulationXpress simulates the design cycle and provides stress results. It also shows critical areas and safety levels at various regions in the faucet. Based on these results, you can strengthen unsafe regions and remove material from overdesigned ones.
|
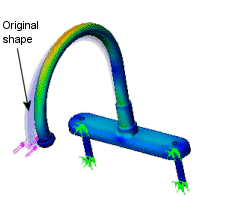 |
Critical regions |
Deformed shape |
SimulationXpress uses the same simulation technology that SOLIDWORKS Simulation uses to perform stress analysis. More advanced simulation capabilities are available within the SOLIDWORKS Simulation line of products. The wizard interface of SimulationXpress uses elements of the full Simulation interface to guide you through a step-by-step process to specify fixtures, loads, material, run the simulation, and view the results.
The accuracy of the results depends on fixtures, loads, and material properties. For results to be valid, the specified material properties must accurately represent the part material, and the fixtures and loads must accurately represent the part working conditions.
SimulationXpress supports the analysis of a single, solid body. It does not support assemblies, multibody parts, or surface bodies.
For lessons on SimulationXpress, see SimulationXpress in the Online Tutorial.