Composite Shells
Composites are a combination of two or more materials that have different properties macroscopically. The number of material phases are usually two and are not soluble in one another. One is the reinforcing phase (e.g. carbon or glass fiber, silica particles) and the other is the matrix phase (e.g. epoxy, vinyl ester) in which the reinforcing phase is dispersed. They can be classified into continuous fiber composites, short fiber composites, and particulate composites.
There are three types of composite options to define the arrangement of plies, thicknesses, material properties, and orientations.
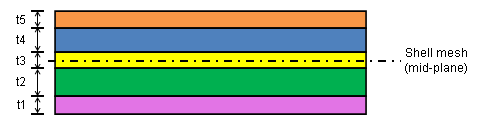
-
A symmetric laminate has a symmetric arrangement of plies (materials, ply orientations, and thicknesses) about the mid-surface. This implies symmetric ply thicknesses, material properties, and material orientations about the mid-plane.
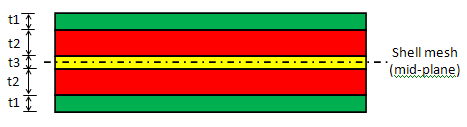
-
The sandwich composite is a special case of the symmetric laminate with three layers. You can use such laminates when higher resistance to bending loads is required. The outer two plies are recommended to be stiffer, stronger, and thinner than the middle ply.
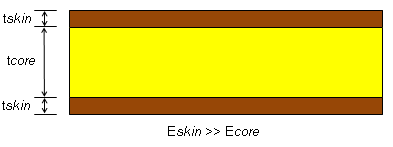
You can use a composite shell for structural members in which you require weight savings. Composite shells also offer improved fatigue strength, corrosion resistance, and thermal conductivity.
You can process models with composite shells in the following ways:
Shell Definition
Ply Stacking Sequence
Ply Angle
Results
In this section you will learn about the following topics: