When the iterative optimization process completes, you view the optimized
geometry of the component in a Material Mass contour
plot.
During a Topology Optimization, the program starts with the given maximum
physical space of a component, which includes all elements, and through an iterative
process determines a new material distribution by removing the "soft" elements that do
not contribute to the stiffness of the component for the particular load scenario,
boundary conditions, and manufacturing controls.
For each element, the optimization algorithm couples the material's Young's
modulus with a relative mass density factor ranging from 0.0001 (for a void element
without any load-carrying capacity) to 1.0 (for a solid element with load-carrying
capacity).
Elements with low relative mass densities (less than 0.3) are considered "soft"
elements. These elements do not contribute to the overall stiffness of the component,
and they can be safely removed. Elements with high relative mass densities (larger than
0.7), are considered "solid". These elements contribute the most to the overall
stiffness (as a measure of the load-carrying capacity) of the component, and they should
remain intact in the final design. The "solid" elements distribute the applied loads
more effectively than the "soft" elements. An isovalue slider adjusts the inclusion of
elements in the Material Mass plot according to their relative
mass density values. The default position of the isovalue slider removes the elements
with relative mass density values less than 0.3. Moving the slider to
Heavy includes all elements, whereas moving the slider to
Light plots only the solid elements, which cannot be
removed.
A Material Mass plot of the optimized car hood
component is shown below. The "soft" elements are removed from the optimized geometry
(image courtesy of Ring Brothers LLC).
In the Material Mass PropertyManager, option
Calculate Smoothed Mesh creates a smooth mesh from the active
Material Mass plot. A smoothed mesh plot of the optimized car
hood component is shown below (image courtesy of Ring Brothers LLC). 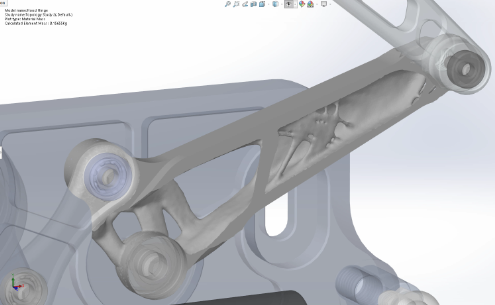
To save the smoothed mesh of the optimized part as new geometry, right-click
the Material Mass plot, and click Export Smoothed
Mesh. You can save the mesh data in a new configuration, or in a new
part file.