The terms "compatible" and "incompatible" mesh refer to the type of mesh continuity on touching geometrical entities that belong to different bodies.
The terms compatible and incompatible mesh apply to the mesh of assemblies and multibody parts that mesh with solid or shell elements, or with both types of elements in a mixed mesh. These terms do not apply to single components (single solid or surface bodies).
Compatible Mesh
In a compatible mesh, touching entities are meshed so that there is a node-to-node correspondence between the mesh of each entity.
Nodes in correspondence can be merged (for a bonded contact), or superposed. For a no penetration contact, node to node contact elements are created between the coincident nodes on the source and target faces.
Results based on a compatible mesh are more accurate that those based on an incompatible mesh.
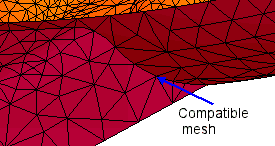 |
This compatible mesh shows coincident nodes at the interface between the surfaces. Simulation merges coincident nodes along the interface for a bonded contact. |
When you request a compatible mesh, the software meshes the parts in the assembly to achieve a smooth mesh transition between any two parts. The nodes along the interface are imprinted one upon another, and they may be merged to ensure a bonded contact. If compatible meshing fails at some interface, the software attempts to generate an incompatible mesh for the two parts at the common interface.
Incompatible Mesh
In an incompatible mesh, there is no a node-to-node correspondence between the mesh of each touching entity. Each entity is independently meshed.
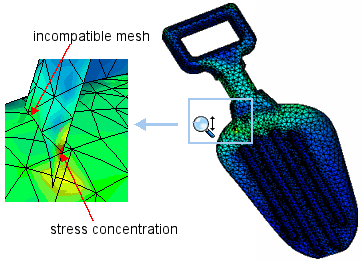 |
This incompatible mesh shows that the nodes at the interface between the surfaces do not correspond. Bonded contact is achieved only with constraint equations. |
You may encounter areas of stress concentration at the interfaces that have an incompatible mesh.