The introduction of distributed coupling enhances the formulation
of pin and bolt connectors.
Distributed coupling allows the faces attached to pin and bolt connectors
to deform, which delivers a more realistic representation of a connector’s behavior.
Distributed coupling for pins and bolts is available for linear static studies only.
In the Connectors PropertyManager,
under Connection Type, select Distributed.
For new pin and bolt connector definitions, the default Connection Type is Distributed. For legacy connector definitions, Connection Type is Rigid.
When you set Connection Type to
Distributed, a distributed coupling
formulation connects a reference node (beam element node of a bolt shank) to a group of
coupling nodes inside the imprint regions of a bolt's head and nut. Distributing
coupling constrains the motion of the coupling nodes to the translation and rotation of
the reference node. Nodes located inside the head and nut imprint areas can deform
relative to each other.
This constraint is enforced in an average sense in a way that enables
control of the transmission of loads through weight factors at the coupling nodes. For
example, the constraint distributes a bolt's pre-load such that the sum of the forces at
the coupling nodes is equivalent to the total pre-load at the reference node. Uniform
weight factors are applied in this case.
The distributed connection produces more realistic stress and
displacement fields at a bolt's head and nut contact areas.
A rigid connection produces stress hot spot areas inside the head and nut
regions of the connected components, because rigid bars introduce high stiffnesses. A
distributed connection eliminates these high stresses.
The image shows two cylindrical components connected by a bolt with a
prestress load of 1,000 N. No-penetration contact exists between the two
components.
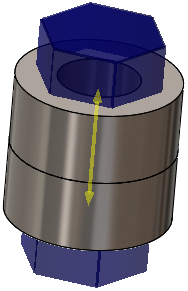