The stress error estimation is based on the principle of the continuity
of the stress field. The stress plot ERR: Energy Norm Error provides
an estimate of the stress field discontinuity from one element to another.
The nodal stresses of each element are averaged to smooth the discontinuity in
the element stresses across the element boundaries. For example, for N elements that
share a common node, Simulation sums the stress values from all elements and divides
them by N to calculate the averaged stress values at that node. Displacement shape
functions (linear or higher-order polynomial) are used to interpolate the new stress
field.
The stress error estimate in each element is defined as the difference between
the element stress and the average of the nodal stresses corrected using the shape
functions. This stress error is used to calculate the energy norm error for each
element.
Select the ERR:Energy Norm Error stress component to
plot the energy norm error for each element. The ERR:Energy Norm
Error plot is only available for static and drop test studies.
The table summarizes the definitions and formulas for the stress error estimates.
Definitions |
Formulas |
Stress error vector |
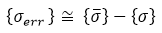
: average
stress vector at a node. If there are N elements that share a
common node, the stress values from all N elements are summed
and divided by N.
: element stress vector at a
node (averaged between the Gauss points within each
element).
|
Stress error estimate of element i based on the energy norm |
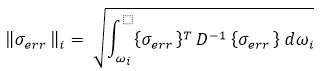
- D: material stiffness matrix or constitutive matrix
- w: element volume
|
Estimate of global stress error (Total Error
Energy) |
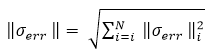
|
Estimate of elemental percentage error (ERR: Energy Norm
Error) |
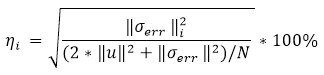
|
Total strain energy |

: elemental strain vector
|
Average Percentage Error (APE) |
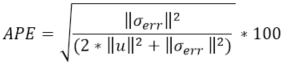 |
- The output file, *.out, reports the Total Strain Energy (TSE), Total
Error Energy (TEE), and Average Percentage Error (APE).
- If the mesh is fine enough such that two neighboring elements have perfectly
continuous stress contours, the stress error at each node would be zero. To
reduce the stress error, refine the mesh in areas of high values of energy norm
error.
References
- A Simple Error Estimator and Adaptive Procedure for Practical Engineering
Analysis by O.C. Zienkiewicz and J. Z. Zhu, International Journal for
Numerical Methods in Engineering, vol. 24, 337-357 (1987)
- An error analysis and mesh adaptation method for shape design of structural
components, by K.-H. Chang and . K. Choi (1991), Computers, and Structures
Vol. 44. No. 6. pp. 1275-1289, 1992 Pergamon Press Ltd.