Connection point management
When a symbol is inserted on a wire, the wire is automatically cut on
the right of the symbol. In the same way, when the wire is placed over
the symbol, it is automatically cut. This is only possible if the symbol
has connection points.
The connection points are placed so that they are superimposed on the
wire when the symbol is inserted. The connection points have an attribute
allowing the number of the manufacturer
part material terminal to be propagated.

|
Menu: Edit symbol >
Connection point |
There are three types of connection points:
Connection
point (by default): A
connection point used for all symbols other than polarity origin-destination.
Incoming/outgoing
connection point: These connection points are directional (incoming
/ outgoing) and exclusively reserved for symbols used for polarity origin-destination.
When inserting connection points, ensure
that the SNAP option is active
and the resolution pitch is compatible with the distance separating the
symbol's circuits, as well as the distance separating two wires (Example:
two phases of a power wire).
The connection points are positioned where the symbol must cut the wire.
To insert a connection point:
1. Select the
circuit the connection point belongs to in the dockable panel.
2. Select the
command in the menu,
3. Turn the
connection point in the right direction (press [Space] on the keyboard
to rotate the connection point according to the angle of the wire),
4. Click on
the insertion point for the connection point in the graphical area.
A message appears informing you when the connection point has been inserted
(N:0-C:0). The number after the
C is the circuit number. The number
after the N is the order number
in the circuit.
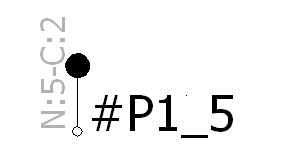
The value allocated to N is
not important; you can have N:6
even if the circuit has only two connection points. All values for N for a given circuit must be compared.
The program then classifies all the connection points for the circuit
according to the value of N.
For a circuit C1, you can have
N:1 and N:4.
N:1 is the first connection point
in the circuit, and N:4 is the
second. When the manufacturer part is allocated, the same principle is
used when allocating the numbers on the material terminal. The number
of the first material terminal will be allocated to the first connection
point on the circuit. The number of the second material terminal will
be allocated to the second connection point on the circuit, and so on
for all of the component's circuits.
A termination type
can be associated with the connection point of the symbol, but if you
assign a manufacturer part on this symbol, the termination type of the
manufacturer part will be applied.
A contextual menu allows you to edit an existing connection point.
Multiple connection points

|
Menu: Edit symbol >
Multiple connection points |
This command is similar to the connection point command except that
circuits can be created simultaneously, helping you place all connection
points after definition.
A dialog box lets you add the circuits that belong to the symbol.

|
Add: Adds
the circuits. |

|
Delete: Deletes
the selected circuits. |

|
Initialize from manufacturer
part: Selects a manufacturer part with its
circuit definition. This manufacturer part can be associated with
the symbol. |
Add the circuit type and indicate the quantity in the Number
of circuits field. Enter the number of terminals on the component,
as well as for each circuit. This data is automatically entered if you
select a manufacturer part. Click OK
to confirm and exit the dialog box.
The connection point is attached to the cursor. The connection points
are placed one after the other, according to the dockable panel instructions.