You can optimize Simulation performance by modeling structural members
with beam elements.
Beam elements are supported for static, frequency, buckling, and nonlinear
studies. Large displacement solution in static studies is not supported for beams. For
the beam formulation to produce acceptable results, the length of the beam can be 10
times larger than the largest dimension of its cross section.
Straight and Curved Beams
Each straight structural member is defined by a straight line
connecting two joints at its ends. A curved structural member is modeled with a
number of straight beams. The cross-section of a beam is assumed to be constant
throughout its length. Internally, the program meshes each beam by creating a number
of beam elements. Each beam element is defined by two end nodes and a cross-section.
When viewing the mesh and results, beam elements can be represented on actual beam
geometry or by cylinders regardless of the actual cross-section.
These images illustrate how a structural member is modeled. One image
shows the structural member and the joints when the structural member is defined as
a beam. The other image shows the mesh, where the beam is subdivided into a number
of beam elements represented by cylinders and beam geometry.
 |
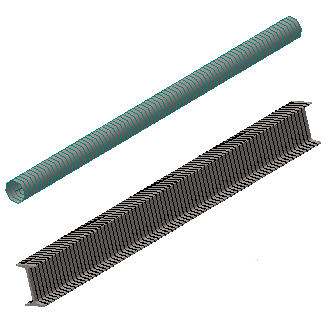 |
Structural member and
joints |
Mesh on cylinders and beam
geometry |
The presence of cutouts, holes, or geometry irregularities along the length of
beams has a negative impact on beam analysis results and also on the 3D rendering of
the beam mesh and results plots. It is recommended to remove any cutouts, holes, or
geometry irregularities from the structural members, before you create the beam mesh
and run the analysis. If you cannot remove any geometry irregularities present along
the length of structural members, use a solid mesh instead of a beam mesh for more
accurate results.
Tapered Beams
You can treat tapered geometries as beams with varying
cross-sectional size along their lengths. The image shows a tapered I-section beam
with cross-sectional size that decreases along the direction shown. The tapered beam
is represented by a straight line (neutral axis) connecting the two end joints. The
lower images show the mesh, where the beam is subdivided into a number of tapered
beam elements represented by cylinders on the left and beam geometry on the right.
Each element consists of two nodes having different cross-sectional areas. The mesh
and the result plots give you a visual indication of the taper along the beam
length.
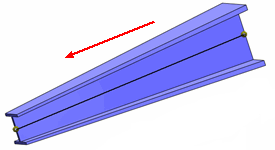
Creating Beams
Structural members that are created as weldment features mesh with
beam elements by default. You can treat these structural members as solids by
selecting their icons in the Simulation study tree and select Treat as Solid. For short structural members (ratio
of length over largest orthogonal cross-sectional distance from the centroid is less
than 3.0), it is recommended to use a solid mesh.
To treat extruded, lofted, mirrored, or imported bodies that have a
constant cross-sectional shape and same or different cross-sectional size across
their length as beams, select their icons in the Simulation study tree and select
Treat as Beam.
The option Treat as Beam
is not available when the ratio of a body's length over the largest orthogonal
cross-sectional distance from the centroid is less than 3.0. This limitation applies
only to structural members created with features such as Extrude, Revolve, Sweep,
etc.
You can define a structural member as a truss or beam in the
Apply/Edit Beam PropertyManager.