Mesh quality plays a key role in the accuracy of the results. The software uses
two important checks to measure the quality of elements in a mesh.
Aspect Ratio Check
For a solid mesh, you achieve the best numerical accuracy with a mesh
that has uniform perfect tetrahedral elements whose edges are equal in length. For a
general geometry, you cannot create a mesh of perfect tetrahedral elements.
Because of small edges, curved geometry, thin features, and sharp
corners, some of the generated elements can have much longer edges than others. When
the edges of an element differ in length substantially, the results are less
accurate.
The aspect ratio of a perfect tetrahedral element is used as the
basis for calculating aspect ratios of other elements. The aspect ratio of an
element is the ratio between the longest edge and the shortest normal dropped from a
vertex to the opposite face, normalized with respect to a perfect tetrahedral.
By definition, the aspect ratio of a perfect tetrahedral element is
1.0. The aspect ratio check assumes straight edges connecting the four corner nodes.
The software calculates the aspect ratio to check the mesh quality.
Example
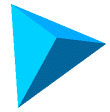 |
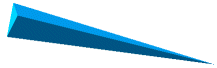 |
Element with aspect ratio
close to 1.0 |
Element with large aspect
ratio |
A good-quality mesh has an Aspect ratio less than 5 for most of its elements (90% and
above). Create a Mesh Quality Plot to plot the Aspect ratio of all elements.
Jacobian Ratio Check
Available for second order mesh elements (high quality solid and
shell mesh).
The Jacobian ratio measures the deviation of an element’s shape from
an ideally shaped element (one that has straight edges with equal lengths). The
Jacobian ratio of a perfect second order tetrahedral element with linear edges is
1.0. The Jacobian ratio of an element increases as the curvature of the element
edges increases to map a curved geometry.
Near extremely sharp or curved boundaries, the edges of an element
can cross over each other and the element becomes distorted, resulting in
self-intersecting geometry. Distorted elements have a negative Jacobian ratio and
produce inaccurate results.
In the Mesh PropertyManager, the
Issue warning for distorted elements
option alerts you if there are distorted elements in the mesh. To remove distorted
elements, first check the model for any geometry irregularities. Refine the mesh in
areas where distorted elements exist.
The Jacobian ratio check considers the Gaussian points located within
each element. The default value in a new study is 16 Gaussian points.
Recommendation: Set Jacobian
check to At Nodes when using
the p-method to solve static problems.
For high-order shells, the Jacobian
check uses 6 points located at the nodes.
A good quality mesh has a Jacobian ratio
between 1 and 10 for the majority of its elements (90% and above). Create a Mesh
Quality Plot to plot the Jacobian ratio of all elements.
For most models, elements at regions of high curvatures have higher
Aspect and Jacobian ratios. If the elements with the highest Aspect and Jacobian
ratios (larger than 10) are away from critical areas for the analysis, it may not be
worthwhile to refine the mesh in these areas. However, for areas that are critical
for the simulation, you can refine the mesh locally to reduce the Aspect and
Jacobian ratios for the poor quality elements and improve the simulation
results.
Depending on the geometry of the model, subsequent levels of mesh
refinement might not improve further the mesh quality and the simulation results.
After each level of mesh refinement, confirm that the mesh quality plots for Aspect
ratio and Jacobian ratio show fewer poor-quality elements. In addition, ensure that
after each successful mesh refinement, the simulation results converge to finite
values.