Enhanced algorithms automatically bond touching entities for the following cases:
- A face or edge of a shell with a solid.
- A face or edge of a shell with another face or edge of shell.
- A face of a solid or shell with a beam that acts as a stiffener.
The beam's body should touch the solid or shell face.
- A face of a solid or shell with a beam joint.
Shells refer to both sheet metals and surfaces. You can apply loads, fixtures, contacts and connectors to the sheet metal and they get transferred to the mid-surface automatically. See Applying Loads and Fixtures to Shells.
To view or edit the shell edge to faces contact definitions, use the option Find shell edge - solid/shell face pairs in the Contact Sets PropertyManager.
For touching faces of sheet metal components that mesh with shells created at mid-surfaces, the program transfers the bonding contact to mid-surface shells automatically.
In cases of bonding contact between sheet metal parts with other surfaces (solids or shells), the bonding algorithm can enforce over-stiffening due to the gap between the mid-surface mesh and the contact surface geometry. The over-stiffening of the bonding contact alters the calculation of the rigid body modes. The program will calculate all rigid modes (with frequency values close to 0), if you eliminate the gap by offsetting the mesh of the sheet metal parts from the mid-surfaces to the contact surface geometry.
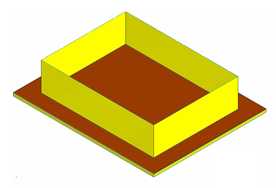 |
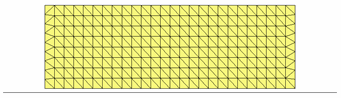 |
Surface edge touching a sheet metal face
|
Side view of mesh (zoomed) |
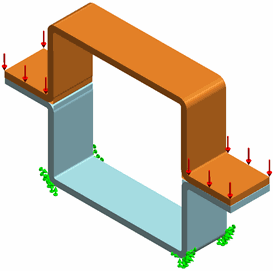 |
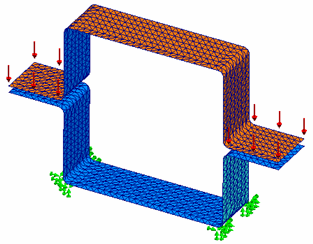 |
Sheet metal faces touching each other
|
View of Mesh at Mid-Surfaces
|
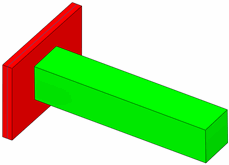 |
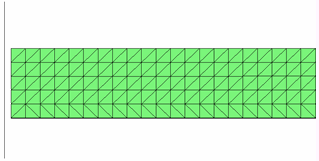 |
Solid face touching a sheet metal face
|
Side view of mesh (zoomed)
|
Bonding between touching structural members with a sheet metal face is also automatically created and transferred to mid-surface shells.
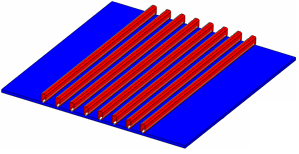 |
 |
Structural members touching a sheet metal face |
Side view of mesh (zoomed)
|
You need to manually define bonding for touching non-planar faces that mesh with shell elements. However, automatic bonding occurs for touching edges of surfaces with non-planar faces.
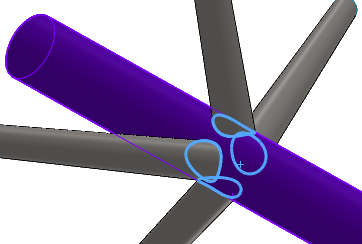 |
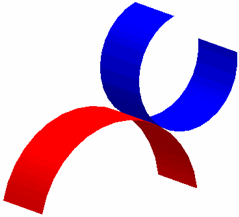 |
Automatic detection of contact sets between solid and shell bodies that intersect at spline surfaces. Use option Find shell edge - solid/shell face pairs. |
Touching non-planar faces of shells. Set the bonded contact manually. |
When beam joints are connected to a neighboring face of a solid or shell, the beam’s actual cross-section is meshed and imprinted on the solid or shell face, creating a more accurate bonding connection.
During meshing, elements are created in the imprinted beam section area. The end beam joint is connected to all elements inside the imprinted section area forming a more realistic representation of the joint.
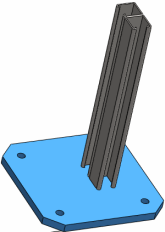 |
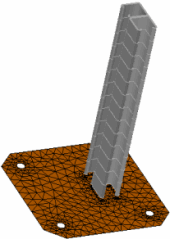 |
Beam-plate joint |
Mesh of the imprinted beam section area on the plate
|
This more realistic formulation of the beam joint - plate bonding connection is not currently available for nonlinear studies. To solve a nonlinear study with beam joint - plate connections, you need to create a new mesh. You cannot copy the existing mesh from a static study to a nonlinear study.