The Global Coordinate System
Directional input refers by default to the global coordinate system (X, Y, and Z), which is based on Plane1 with its origin located at the Origin of the part or assembly. Plane1 is the first plane that appears in the FeatureManager design tree and can have a different name. The reference triad shows the global X-, Y-, and Z-directions.
The figure below illustrates the relationship between the global coordinate system and Plane1, Plane2, and Plane3.
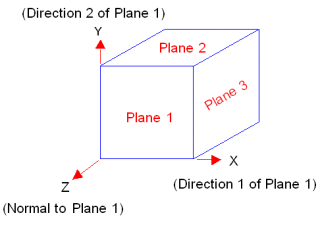
Where X is Direction 1 of Plane 1, Y is Direction 2 of Plane 1, and, Z is the Normal to Plane 1.
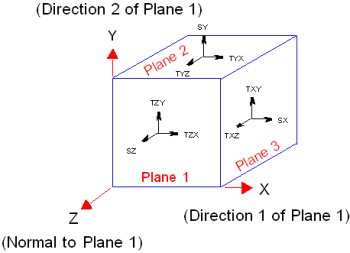
|
Stress components in the global coordinate system |
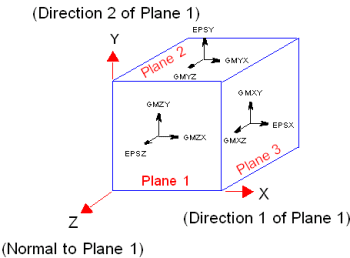
|
Strain components in the global coordinate system |
The global coordinate system can be displayed on any plot by right-clicking its icon and selecting Axes.
Local Coordinate Systems
Local coordinate systems are coordinate systems other than the global coordinate system. You can specify restraints and loads in any desired direction. For example, when defining a force on a cylindrical face, you can apply it in the radial, circumferential, or axial directions. In this case, you need to select an axis as a reference geometry.
Similarly if you choose a spherical face, you can choose the radial, longitude, or latitude directions to apply restraints.
When viewing results, you can also use reference planes and axes. For example, you can view stresses on a cylindrical face in the radial direction.
Using Reference Planes and Axes. You can use reference planes and axes to define orthotropic material properties or apply directional loads and restraints.
- Using Reference Planes. A reference plane defines a Cartesian coordinate system as illustrated in the figure.
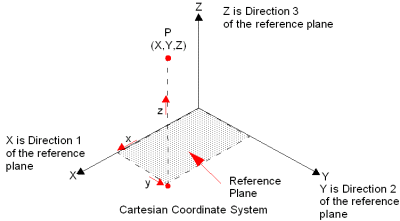
- Using Reference Axes. A reference axis defines a cylindrical coordinate system as illustrated in the figure.
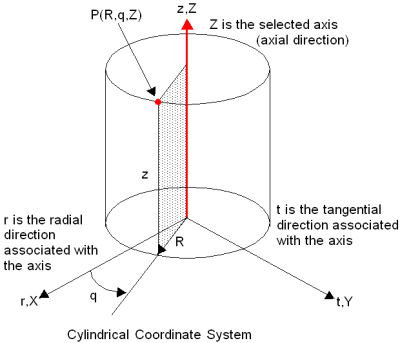
Refer to the Loads and Restraints section for more details.