General
The following are general guidelines for specifying interaction
conditions:
- Check for interference between components before meshing. To
detect interference in an assembly, click . Interference is allowed only when applying the Shrink Fit interaction type. The Treat coincidence as interference option allows
you to detect touching areas.
- Use the Local
Interactions PropertyManager to define interactions between
solids, shells, and beams.
- Select Automatically find local
interactions (Local
Interactions PropertyManager) to detect interactions for
components that are touching or are not touching, but are within a certain
clearance.
- Specify global, component, and local interactions efficiently to
define the actual behavior of components for a successful simulation. Assign the
most common interaction type globally, and then define component-level and
local-level interaction conditions as required.
- Local interactions settings override component-level
interactions, while component-level interactions override global-level
interactions.
- Remesh the study after editing or defining contact
conditions.
Bonding
- Bonding ensures the continuity of components and the transfer of
applied loads between two entities. You can bond a face or an edge to any other
face or edge. The mesh at the touching boundaries of the bonded entities does
not have to be continuous.
- For assembly components that share common mesh nodes but failed
to
bond,
select Remesh failed parts independently
(Default Options - Mesh dialog
box).
- SOLIDWORKS Simulation enforces bonded interactions to qualified
geometric entities that are not initially touching based on specified
clearances. These settings ensure that you can run simulations, even for models
with slightly imperfect geometries. You can customize the default clearances to
better fit your models.
- When bonding solid faces through the global contact condition,
select Enforce common nodes between touching
boundaries (Default Options - Interactions) to generate a
continuous mesh on the touching boundaries.
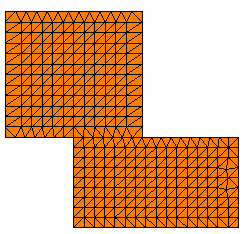
- In cases of bonding between a sheet metal and other surfaces
(solids or shells), a gap exists between the mid-surface mesh and the surface
geometry because of the shell thickness.
An
algorithm for the Surface to
surface bonding formulation for Linear static, Frequency, and
Buckling studies detects the rigid body motion caused by the gap, and ensures
the
accuracy of the solution.
For
the Node to surface simplified bonding
formulation and for all bonding types in Nonlinear studies, such enhancement is
not yet implemented.
Consider the following model:
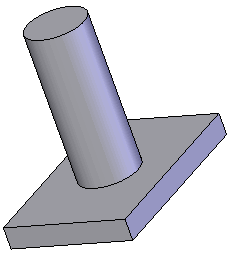
- A global bonded interaction bonds the whole circular face of the
cylinder to the plate.
- If the cylinder is connected to the plate by welding its edge
only, then specify the global interaction to Free, and bond the face of the plate to the edge of the
cylinder by defining a local interaction set.
- If a small clearance exists, you can specify the appropriate
Gap range for bonding (Local Interactions PropertyManager) to bond the
cylinder's face or edges to the plate.
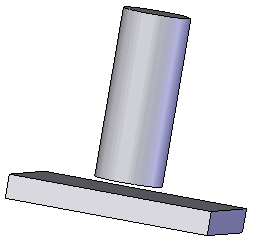
Static and Nonlinear Studies
- Contact is a common source of nonlinearity. Although nonlinear
studies are preferred for solving contact problems, you can use static studies
to solve contact problems with small and large displacements.
- The properties
dialog
box of static and nonlinear studies
provides
an option to use large displacements. Use the small displacement formulation
only if the expected motions are small and the parts are independently stable in
directions other than the primary contact direction.
SOLIDWORKS Simulation automatically detects when large displacements occur
and prompts you to activate the large displacement flag. Select Yes to rerun the simulation with the large
displacement option. Select No to run
the simulation with the small displacement formulation.
When you use static studies with the large displacement
option to solve contact problems, the results are available only at the last
solution step. In nonlinear studies, results are available at every solution
step.
- Use
Shrink Fit in the
Local Interactions PropertyManager to
define a shrink fit interaction condition between initially interfering
components.
- In general, the Surface to
surface contact formulation is more accurate than the Node to surface contact option. However, it
takes longer to solve and may not converge when the contact area becomes too
small. In such cases, use the Node to
surface option.
-
The Node to node
contact formulation
is
no longer
available.
When you open models with legacy node-to-node contact definitions,
SOLIDWORKS Simulation converts them to Node to
surface contact during the analysis.
Thermal Studies
- The Bonded, Thermal resistance, and Insulated interaction conditions are available.
Free faces (faces without any boundary conditions) are insulated. A free face is
thermally similar to a face with a zero temperature gradient in the normal
direction. Faces of thermal symmetry can be modeled as free faces. Heat can flow
parallel to the face but cannot flow normal to it.
- Use the Surface to
surface formulation to simulate thermal resistance.
Buckling Studies
Only the Bonded and Free interaction options are available.
Frequency Studies
Only the Bonded and Free interaction options are available. Use caution
when specifying the Free option and
interpreting results associated with it as the parts are considered disjointed.
Linear Dynamic Studies
The Bonded and Free interaction options are available for all
linear dynamic study types.
Drop Test Studies
The Bonded, Free, and Contact options are available. Only the Node to surface contact formulation is available.