Plasticity von Mises Model
The yield criterion can be written in the form:
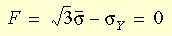
where s
is the effective stress and sY is the yield stress from uniaxial
tests. The von Mises model can be used to describe the behavior of metals.
In using this material model, the following considerations should be noted:
Small strain plasticity is assumed when small
displacement or large displacement is used.
An associated flow rule assumption is made.
Both isotropic and kinematic hardening rules are
available. A linear combination of isotropic and kinematic hardening is
implemented when both the radius and the center of yield surface in deviatoric
space can vary with respect to the loading history.
The parameter RK
defines the proportion of kinematic and isotropic hardening.
For pure isotropic hardening, the parameter
RK has the value 0. The radius
of the yield surface expands but its center remains fixed in deviatoric
space.
For pure kinematic hardening, the parameter
RK has the value 1. The radius
of the yield surface remains constant while its center can move in deviatoric
space.'
A bilinear
or multi-linear uniaxial stress-strain curve for plasticity can be input.
For bilinear stress-strain curve definition, the yield strength and elastic
modulus are input through the Material
dialog box. For multi-linear stress-strain curve definition, a stress-strain
curve should be defined.
When you define a stress-strain curve, the first
point on the curve should be the yield point of the material. Material
properties like elastic modulus, Yield strength, etc will be taken from
the stress-strain curve when it is available and not from the material
properties table in the Material
dialog box. Only Poisson's ratio (NUXY)
will be taken from the table.
Defining stress-strain curves
is not supported by drop test studies.
The SIGYLD
and ETAN parameters for bilinear
stress-strain curve description can be associated with temperature curves
to perform thermoplastic analysis.
The use of NR
(Newton-Raphson) iterative method is recommended.
The Huber-von Mises model can be used with the solid (draft and high
quality) and thick shell (draft and high quality) elements.
Thermo-plasticity is not available with shell
elements.
The following figure depicts a typical stress-strain curve of a plastic
material:
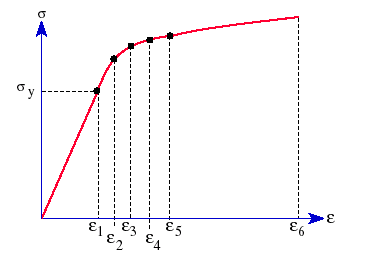
Large Strain Analysis
In the theory of large strain plasticity, a logarithmic strain measure
is defined as:

where U
is the right stretch tensor usually obtained from the right polar decomposition
of the deformation gradient F (i.e., F
= R
U,
R
is the rotation tensor). The incremental logarithmic strain is estimated
as:

where B(n+1/2) is the strain-displacement
matrix estimated at solution step n+1/2
and Du
is the incremental displacements vector. It is noted that the above form
is a second-order approximation to the exact formula.
The stress rate is taken as the Green-Naghdi rate so as to make the
constitutive model properly frame-invariant or objective. By transforming
the stress rate from the global system to the R-system,
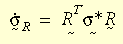
The entire constitutive model will be form-identical to the small strain
theory. The large strain plasticity theory is applied to the von Mises
yield criterion, associative flow rule and isotropic or kinematic hardening
(bilinear or multi-linear). Temperature-dependency of material property
is supported by bilinear hardening. The radial-return algorithm is used
in the current case. The basic idea is to approximate the normal vector
N by:
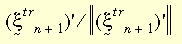
where,

The following figure illustrates the above two equations.
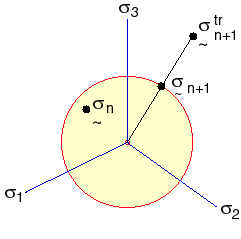
The element force vector and stiffness matrices are computed based on
the updated Lagrangian formulation. The Cauchy stresses, logarithmic strains
and current thickness (shell elements only) are recorded in the output
file.
The elasticity in the current case is modeled in hyperelastic form that
assumes small elastic strains but allows for arbitrarily large plastic
strains. For large strain elasticity problems (rubber-like), you can use
hyperelastic material models such as Mooney-Rivlin.
Cauchy (true) stress and logarithmic strain
should be used in defining the multi-linear stress-strain curve.
Comparison of
Tresca and von Mises Criteria for Plasticity